WHY IS NON-DESTRUCTIVE CRACK TESTING NECESSARY?
In recent years, non-destructive material testing has been firmly established in process monitoring. Due to it’s efficient performance, this inspection program has become essential for comprehensive process control.
If components in safety-critical applications fail or do not meet the requirements, the consequences can cause extensive costs. For example, if a suspension part breaks during operation, it will be immediately life-threatening. Therefore, the automotive industry and many other defined standards for these type of components. This ensures continuous and in-depth inspection of safety-related components during the manufacturing process.
The classic part defect is the crack found on the surface of the material. The eddy current test is usually used here. This is because even the smallest crack that does not cause problems at first may expand under permanent load. In the worst case, this may cause the component to fail. The most common types of defects found in surface inspection, in our experience, are cracks, cavities, dents, grinding burn, hard spots, soft spots and magnetic inclusions (remanences).
Depending on the application, different test methods are used. The most important influencing factors are the test material, size, defect pattern and test task, as well as the required cycle time and available budget. Based upon this, different methods are available depending on the testing task: Visual inspection (VT), Dye penetrant testing (PT), Eddy current testing (ET), Thermographic tests (TT), Magnetic particle testing (MT) and Ultrasonic testing (UT).
HOW CAN QLTY SOFTWARE SPEED YOUR PROCESS AND TRACK PRODUCTS QUALITY?
QLTY Software is built for every phase of your products development process to plan, track and release products with the highest possible quality. Storing product-related information of non-destructive crack testing has never been easier and more efficient.
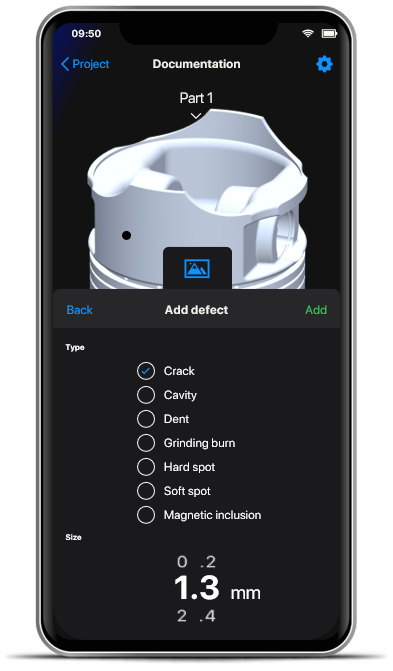
Create individual projects – tailor-made for your product and process
Choose crucial defect information, just like the type and size of the discovered defect and plan product-specific requirements such as area-specific limit values for each defect type. All defects are classified as valid or invalid based on the data-base.
Data entry
The data entry can be made on a component-specific basis. When crack indication is done, the tester switches to cloud documentation in the software.
Besides storing the chosen crucial information QLTY could be your central data management of all test-related images, documents, notes, videos, test reports and templates.
Prioritize and pay attention to the right details
Within the blink of an eye, documented defects are ready for analysing – thanks to the cloud documentation. Discuss your results in full context with complete visibility and make data-driven decisions with your team.
Review of data
Whether you’re analyzing a complete inspection lot, or some carefully selected parts, QLTY reveals areas for improvement at first sight. Which product area needs your attention the most? What is the fastest way to increase product quality?
For your team it has never been easier and more efficient to detect key points of the available information. Create your own filters that answers your most important issues.
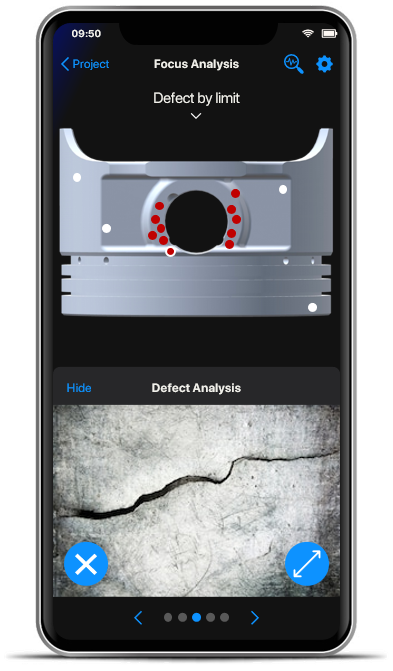
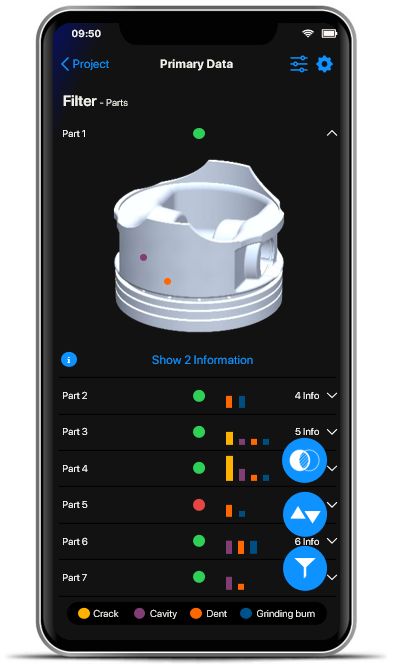
Ship products of highest quality
With quick access and always up-to-date data it has never been easier to pick the right parts for shipping. And what about material analysises with the parts not shipped?
Release of products
With QLTY you basically create 3d-digital twins as an exact reflection of the products you ship. Use the cloud documentation for quality controls and verifications. Make sure your team doesn’t face avoidable recalls.
Be prepared for what’s coming in the future with the documentation you do today. Store data of each product through archiving, available any time during the life-cycle of the product.
Improve product quality based on real-time and visual data
How much time passes before collected data arrives at the right place? How much effort does your team put into data processing before they can put it to use? The answer is as simple as unsatisfactory: too much.
Analyse data
Our software solutions can help you analysing impacts of changes in the production process to your products quality output. It provides an accurate understanding of the implications, which helps the team make informed quality decisions about which changes to approve.
All you need to do is simply provide the data. Everything else is up to QLTY.
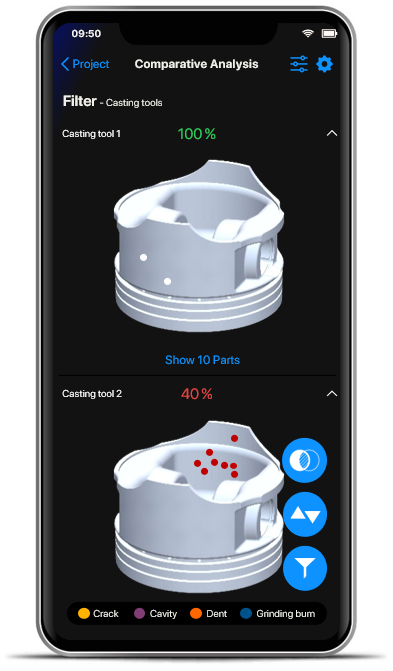
More power and possibilities with QLTY
QLTY Software comes with many intelligent features to speed your process. Keep track of all your projects with cloud documentations, so you can access them anywhere – even offline.
Troubleshooting
When nothing goes right, go with QLTY – back on track in no time.
Custom filters
Create your own filters that answers your important issues.
Mobile applications
Move quality forward from anywhere with QLTY mobile.
User administration
Manage user rights and permissions for each and every project you work on.
Customizable workflows
Create customizable workflows that fit’s your style of quality.
Cloud application
Cloud is more than a deployment change. It’s a new attitude.
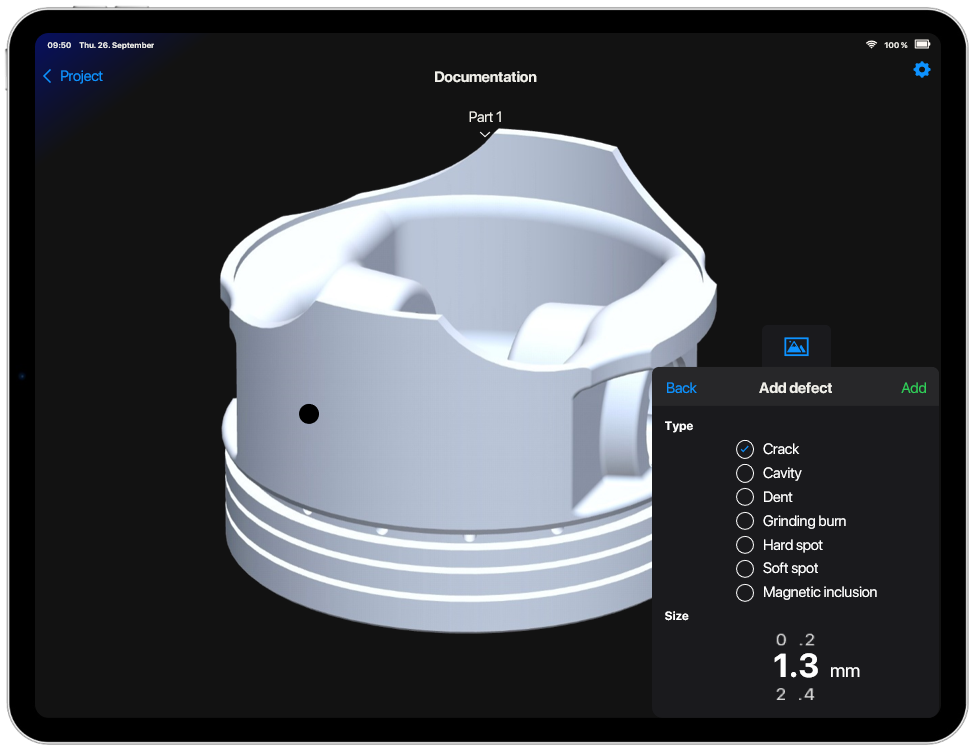
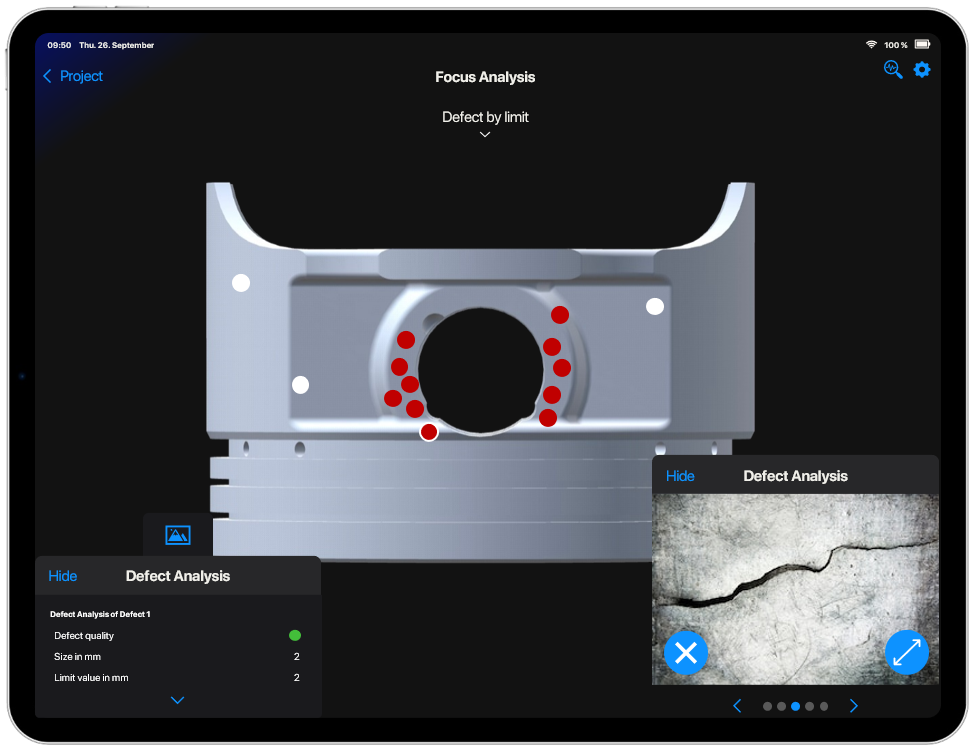
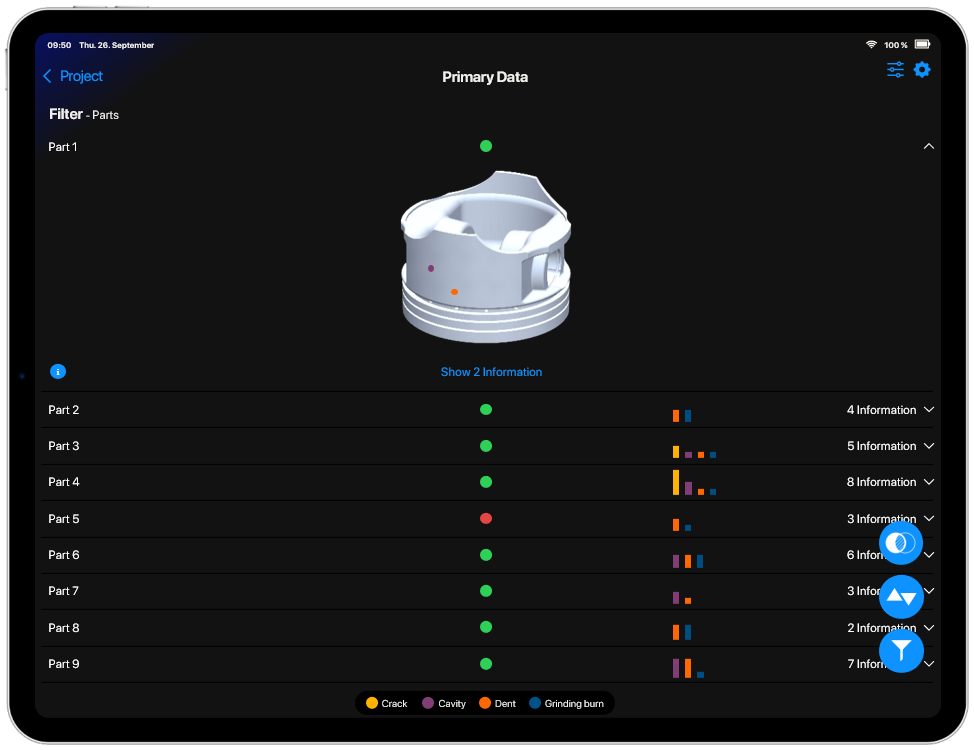
